Embodied Carbon: A Tool for Renovations & Retrofits
So, your building is creaky, an energy hog, or just plain outdated? There are many ways to go about “improving” your building – from its energy efficiency to its user-friendliness, and so much more. One of the biggest topics nowadays is sustainability, and particularly decarbonization. Believe it or not, this does not just apply to new buildings – existing buildings offer potentially even more opportunities for improvement and savings. A powerful tool when talking about an existing building is its embodied carbon. Embodied carbon relates to the environmental effect a material has throughout its lifecycle. There are endless opportunities to avoid significant embodied carbon emissions by opting to renovate an existing building instead of going the new construction route. Finding the happy balance between what to renovate and what to leave as-is, will help mitigate some of the capital costs associated with the renovation, reduce utility bills, improve air quality, and enhance its overall sustainability.
Embodied carbon is defined as the greenhouse gas emissions (GHG’s) resulting from the extraction, production, transportation, installation, maintenance, and disposal or reuse of materials throughout their lifecycle. This is different from operational carbon, which refers to the greenhouse gas emissions resulting from a building’s energy consumption. Embodied carbon and operational carbon combine to represent the net environmental effect of a building (using GHG’s as a metric) through its life cycle. For this article’s purposes, we will focus on embodied carbon, as retrofits and renovations have great potential for avoiding significant carbon emissions through re-use of existing materials. According to the World Green Building Council, the renovation of an existing building already accomplishes the first commitment principle for embodied carbon – “prevent.” This is because the current state of an existing building is essentially holding a sink of carbon. By simply deciding to retrofit or renovate your building – rather than new development – you are avoiding increasing embodied carbon from the start.
Some Practical Strategies
There are a few tips that can help facility managers and project teams lower their renovation’s embodied carbon. (Please note that this is not a comprehensive list – there are many ways and perspectives to reduce a building’s embodied carbon).
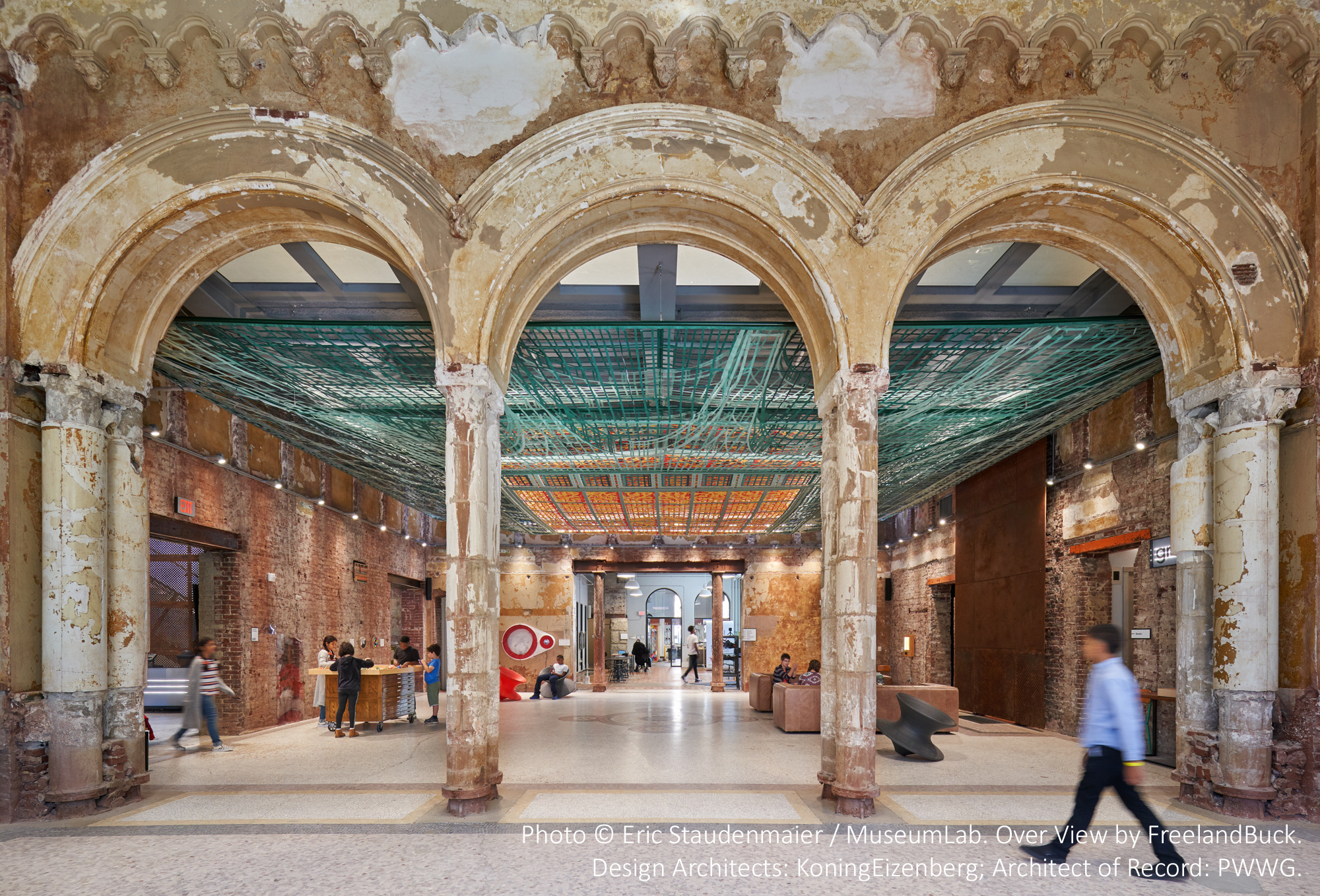
1. What Retrofitting an Existing Building Means for You
When you choose to retrofit an existing building, you are giving new life to a building that already had its own embodied carbon. In reusing most of the building’s existing structure and elements, you avoid the use of new materials and their associated carbon emissions, cutting capital costs and avoiding additional embodied carbon significantly compared to demolishing and rebuilding new. Careful analysis of what to keep and what to replace in your existing building will help further lower the embodied carbon in your renovation project.
2. Setting Clear Goals
There are many approaches to lowering a project’s embodied carbon. The best strategy for your project will depend upon what your aim is with the renovation. Some strategies may include improving operational efficiency, repurposing the building for a new use, and improving current occupant experience of the space. Clarifying the project goals first and foremost is essential, along with strategizing what that means for the design team, the building occupants, and the future version of the building. Strategies to aid with this process can include energy modeling, ethnographic studies, building conditions survey, and more. Having clear goals for the renovation project will allow for each design choice to be evaluated properly to align with your greater vision. This will help to identify strategies for embodied carbon reduction that work alongside project timing and scope rather than hinder or create unnecessary complications.
3. Choosing Low-Carbon Materials
This step involves a balanced analysis of the carbon content and the long-term effectiveness of each new material going into the building. If a product isn’t made well or lacks durability, the initial embodied carbon will be surpassed by the carbon cost of replacing it. It should also be noted that traditionally-used materials have low-carbon alternatives that are effective options to be considered – and can even be a more durable and efficient counterpart. A low-carbon material is defined as material with lower embodied carbon footprint than traditional materials – meaning they require less energy and resources be produced (generating fewer greenhouse gas emissions). This can vary from recycled materials to bio-based materials (made from natural materials, such as bamboo, hemp, or straw).
4. Taking a Holistic Approach
Taking a holistic approach for embodied carbon reduction will mitigate risks and problems arising from competing goals. This can be done by setting a clear strategy, collecting comprehensive data, modeling the life cycle, and conducting trade-off analyses between embodied carbon vs operational carbon and cost vs benefits. Such a holistic approach, if implemented by project teams, will maximize preservation of reusable building elements, encourage collaboration of all stakeholders along the value chain, and help to overcome the current lack of benchmark data for retrofit projects.
It is important to celebrate the choice to renovate your building – that in and of itself is a great accomplishment in terms of embodied carbon reduction. From here, the renovation is an opportunity for imagination and creativity – there are so many approaches to take in reimagining the building. A building’s embodied carbon is a valuable analytical tool that can be used to enhance its longevity, efficiency, and sustainability.
Kristy M. Walson, PE, LEED Fellow, BEMP – Principal
direct phone: 407.593.4867
Kristy Walson, Principal and Building Science Practice Lead at BranchPattern, champions a transformative approach to sustainable design and decarbonization. Kristy merges her engineering expertise and passion for a regenerative future to propel the built environment toward a low-carbon, equitable world. An accomplished leader with credentials including LEED Fellow and BEMP, Kristy heads BranchPattern's Analytics Department, overseeing vital Building Performance Modeling and Materials initiatives that focus on reducing both operational and embodied carbon. Her active roles in the U.S. Green Building Council, ASHRAE, and industry accolades like AIA's COTE Top 10 jury reflect her commitment to advocacy and innovation in sustainable building science.
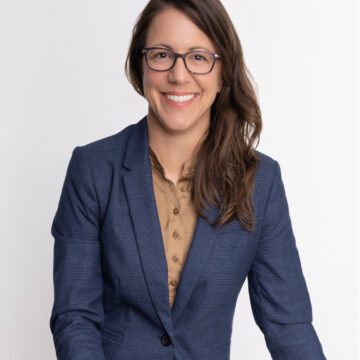
Eliana Peralta-Sapienza, LEED AP BD+C, WELL AP, EDGE Expert – Associate
direct phone: 518.650.2860
Eliana Peralta-Sapienza, a Building Performance Analyst at BranchPattern, is dedicated to enhancing energy efficiency and reducing carbon emissions in buildings, driven by her mission to leave a positive environmental legacy. With a Master’s in Sustainable Buildings and Environments and credentials like LEED BD+C, WELL AP, and EDGE Expert, Eliana brings a global perspective from her work across the UK, Ireland, Azerbaijan, and the Dominican Republic.
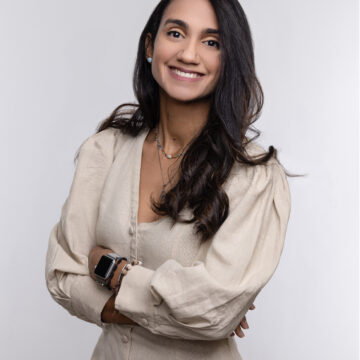
Sussan Jarvis – Associate
direct phone: 601.927.9114
Sussan Jarvis, a Project Executive on BranchPattern’s Materials Team, leads with innovative thinking and a dedication to measurable sustainability. Specializing in Carbon Accounting and whole-building life cycle assessments, Sussan leverages her background in architecture and technical expertise to push sustainable practices to the forefront. Her global perspective, enhanced by degrees from the National University of Architecture and Construction of Armenia and Sheffield Hallam University, empowers her to create transformative systems that streamline processes and enhance building sustainability.
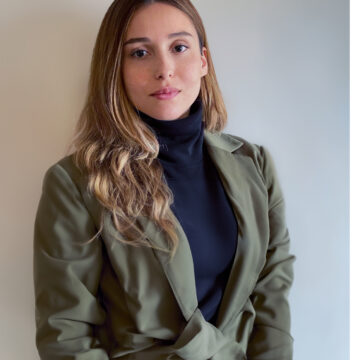
View More Resources
Benefit from our expertise
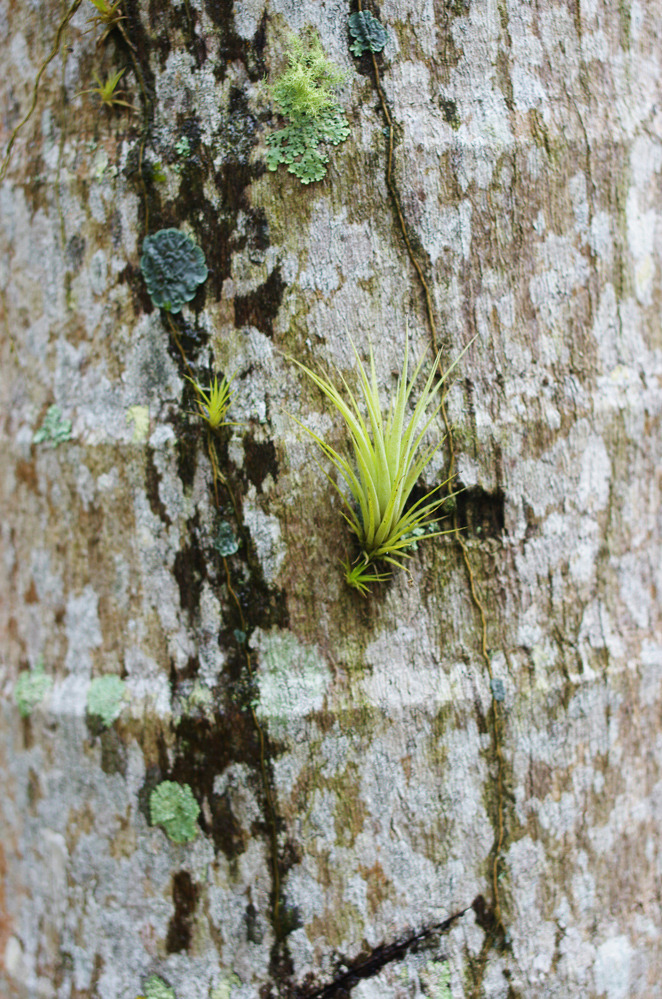
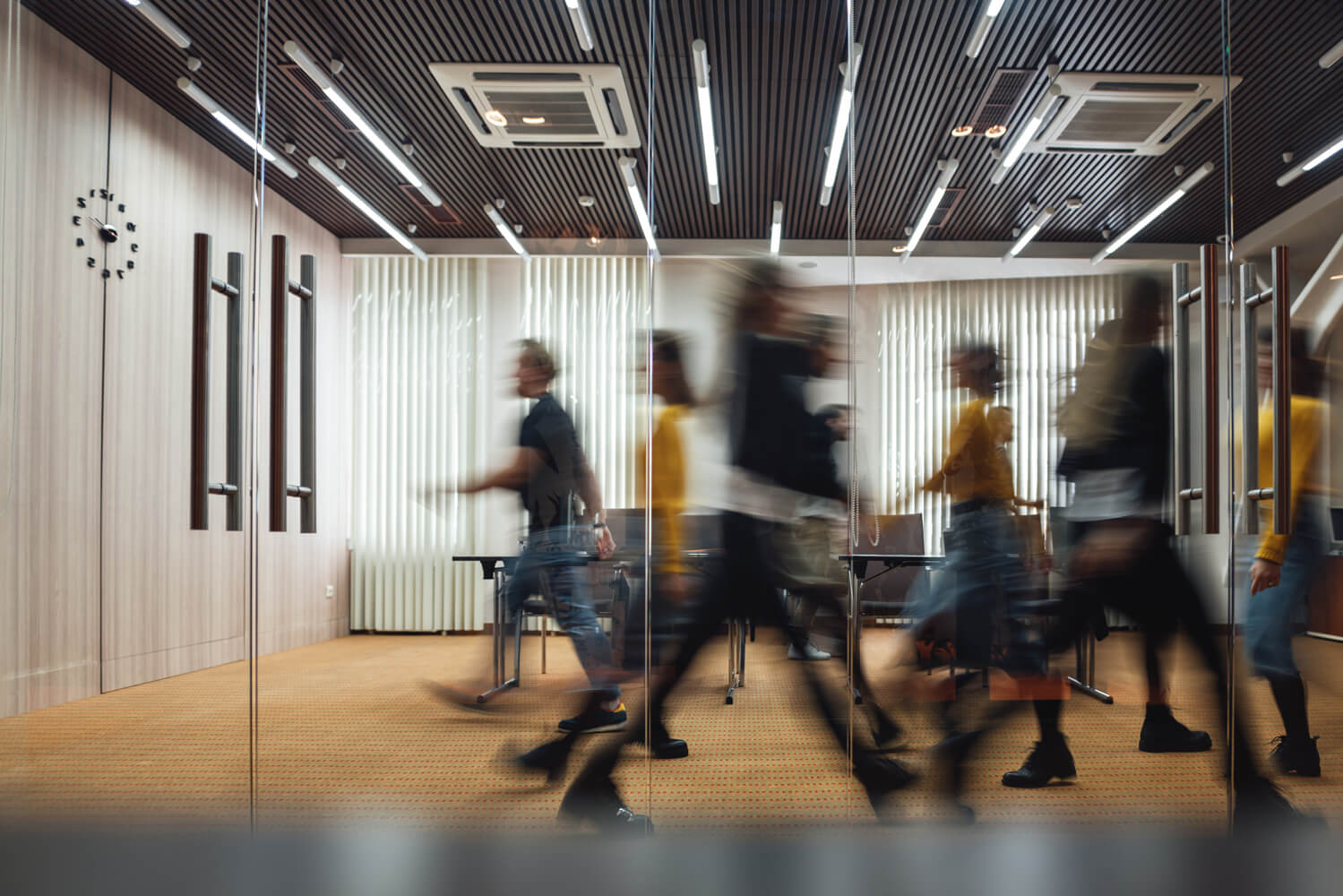